Produkcja materacy: jak powstaje materac?
Zaktualizowano 07. marca 2025
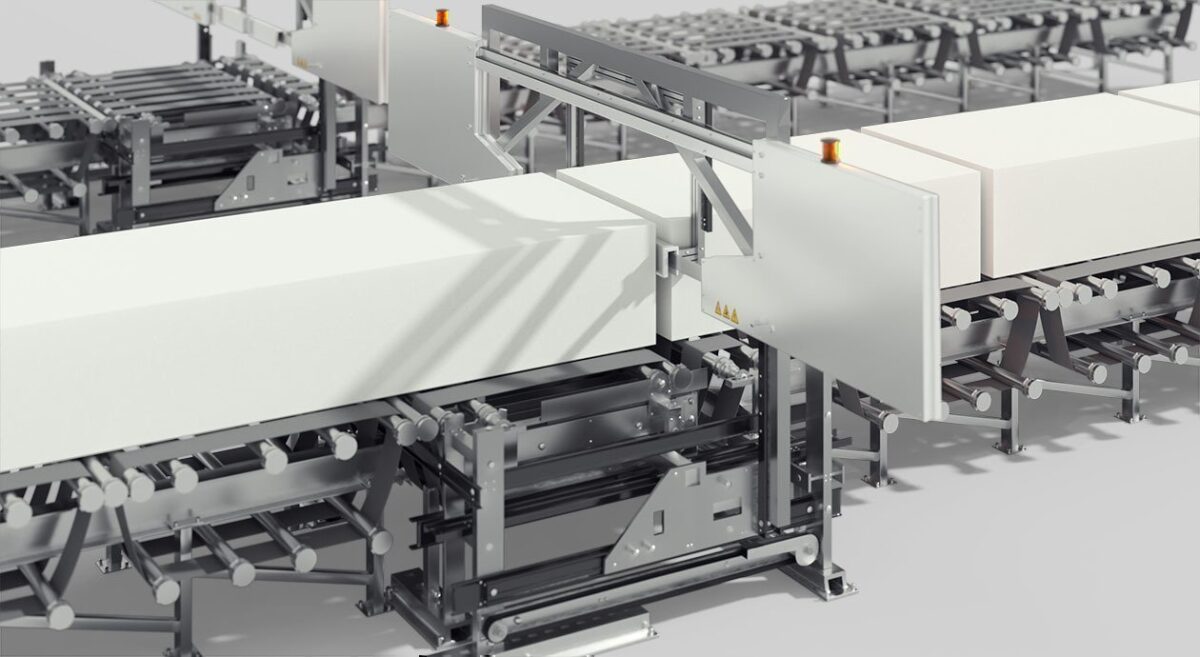
Wielu producentów materacy niechętnie zdradza tajniki swojej produkcji. Dokładna „receptura” wytwarzania ich materacy pozostaje zwykle tajemnicą. Każdy producent stosuje własne podejście do procesu produkcji materacy oraz do doboru materiałów. Dobrzy producenci materacy skupiają się na najważniejszych aspektach i dokładają wszelkich starań, aby każdy, nawet najmniejszy etap produkcji był jak najbardziej efektywny. Choć proces produkcji materacy może wydawać się skomplikowany, jego podstawowa zasada jest prosta do wyjaśnienia.
Rdzeń – najważniejszy element w produkcji materacy
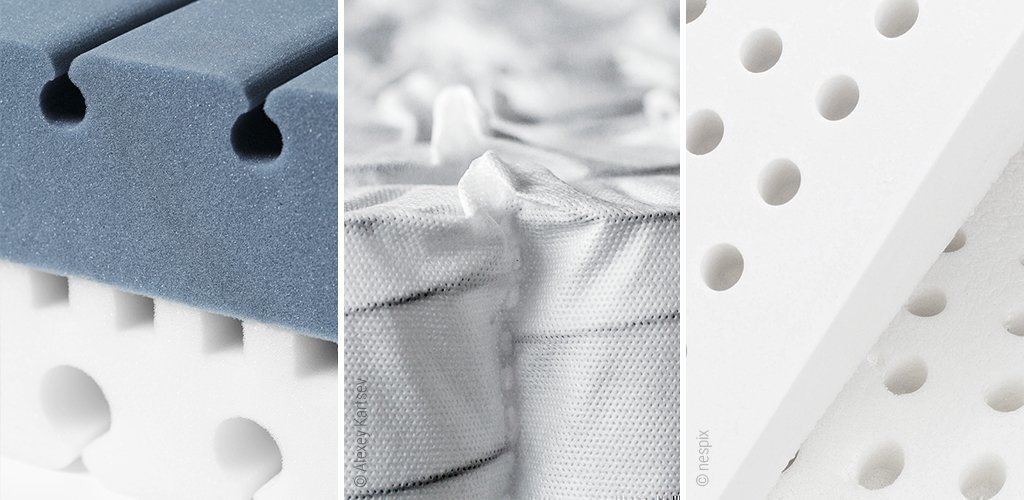
Wnętrze każdego materaca to jego rdzeń, który ma największy wpływ na komfort leżenia. Podczas gdy dawniej materace były wypełniane różnymi nietypowymi materiałami, dziś dominują trzy główne rodzaje rdzeni: piankowe, lateksowe i sprężynowe. Większość sprzedawanych obecnie materacy to modele piankowe, następnie sprężynowe, a najmniejszy udział mają materace lateksowe. W przypadku pianki i lateksu rdzeń może składać się w 100% z tych materiałów, natomiast rdzenie sprężynowe zawsze wymagają dodatkowej warstwy amortyzującej, najczęściej z pianki, aby powierzchnia leżenia była miękka i wygodna.
Rdzeń piankowy
Rodzaje rdzeni piankowych
Pianki stosowane w produkcji materacy różnią się pod względem jakości i właściwości. Najprostsze to tzw. pianki komfortowe, często określane jako pianki PUR. PUR oznacza poliuretan – tworzywo sztuczne, z którego wykonane są wszystkie pianki materacowe. Pianki komfortowe są produkowane metodą spieniania na gorąco. Wyższej jakości pianka HR (wysokoelastyczna) jest spieniana na zimno, co zapewnia jej większą trwałość i odporność na odkształcenia. Na bazie pianki HR opracowano także bardziej zaawansowane materiały, takie jak pianka QXSchaum® stosowana w materacach BODYGUARD®. Inne rodzaje pianek to pianka żelowa oraz wrażliwa na temperaturę pianka visco.
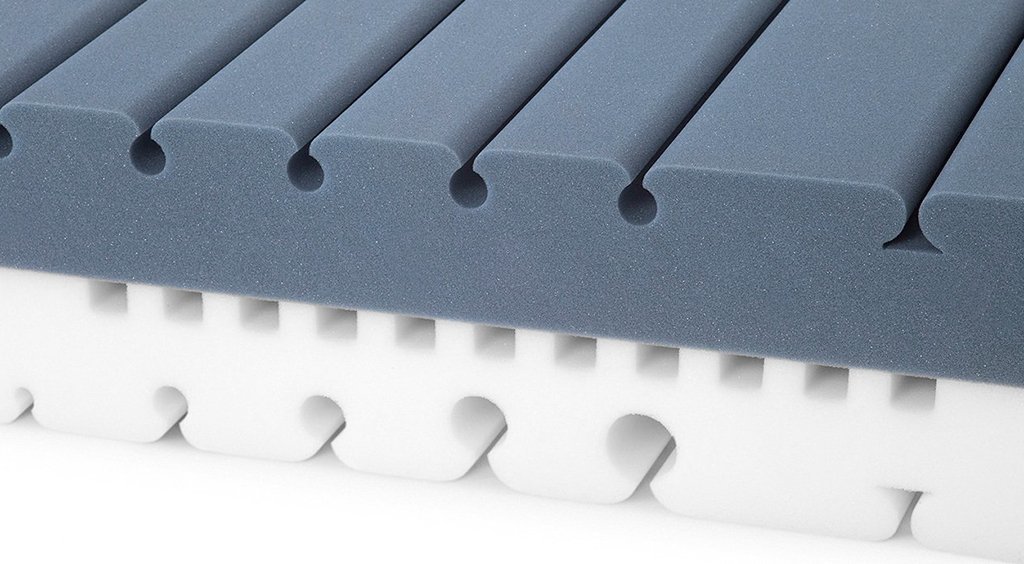
Proces produkcji rdzenia piankowego
Do produkcji pianek poliuretanowych wykorzystuje się głównie dwie substancje: izocyjanian i poliol. Ich zmieszanie powoduje reakcję chemiczną (polimeryzację), w wyniku której powstaje poliuretan. Jeśli w trakcie tej reakcji obecna jest wilgoć, dochodzi do wydzielania gazów, które spieniają poliuretan. Stopień wilgotności i temperatura w momencie spieniania wpływają na końcową strukturę pianki.
Rdzenie piankowe nie są formowane pojedynczo, lecz wycinane z dużych bloków pianki, które mogą osiągać rozmiary wagonu kolejowego. Właściwości pianki w jednym bloku mogą się różnić, co pozwala na uzyskanie zarówno miękkich, jak i twardszych fragmentów. Najlepsi producenci materacy dążą jednak do uzyskania jak najbardziej jednolitej struktury pianki, aby zawsze móc zapewnić tę samą jakość.
Po wycięciu rdzenia wprowadza się w nim nacięcia, które określają, w jakich miejscach materac ma się uginać. Następnie rdzeń poddaje się intensywnemu sprasowaniu, aby usunąć pęcherzyki powietrza i uzyskać bardziej oddychającą strukturę.
Produkcja materacy a gęstość pianki
Im więcej pęcherzyków powietrza powstaje podczas spieniania, tym więcej porów pozostaje w piance po jej utwardzeniu. Zbyt wiele i zbyt duże pory mogą jednak osłabić strukturę pianki. Często w branży materacowej mówi się, że wysoka gęstość pianki (tzw. gęstość objętościowa) jest oznaką wysokiej jakości. Jednak nie jest to takie proste: mniejsza liczba porów oznacza również ograniczoną cyrkulację powietrza. Dlatego nie tylko ilość porów, ale także ich struktura mają znaczenie dla stabilności materaca. Pianka QXSchaum® w materacu BODYGUARD® udowadnia, że stosunkowo niska gęstość może iść w parze z wysoką trwałością i stabilnością kształtu.
Rdzeń sprężynowy
Rodzaje rdzeni sprężynowych
W produkcji materacy stosuje się trzy główne rodzaje sprężyn: klasyczne sprężyny bonellowe, sprężyny kieszeniowe oraz sprężyny typu multipocket. Sprężyny bonellowe, wynalezione w XVIII wieku, pierwotnie stosowano w meblach tapicerowanych. Dopiero gdy połączono je drutem, zaczęły być wykorzystywane w materacach. Dzięki temu sprężyny reagują na obciążenie wspólnie, co daje uczucie miękkości. W przypadku materacy kieszeniowych każda sprężyna umieszczona jest w oddzielnej tkaninowej kieszeni, co redukuje hałas i zapewnia lepsze dopasowanie do ciała. Sprężyny multipocket mają natomiast bardziej zaokrąglony kształt i łatwiej się uginają, co zapewnia wyższy komfort.
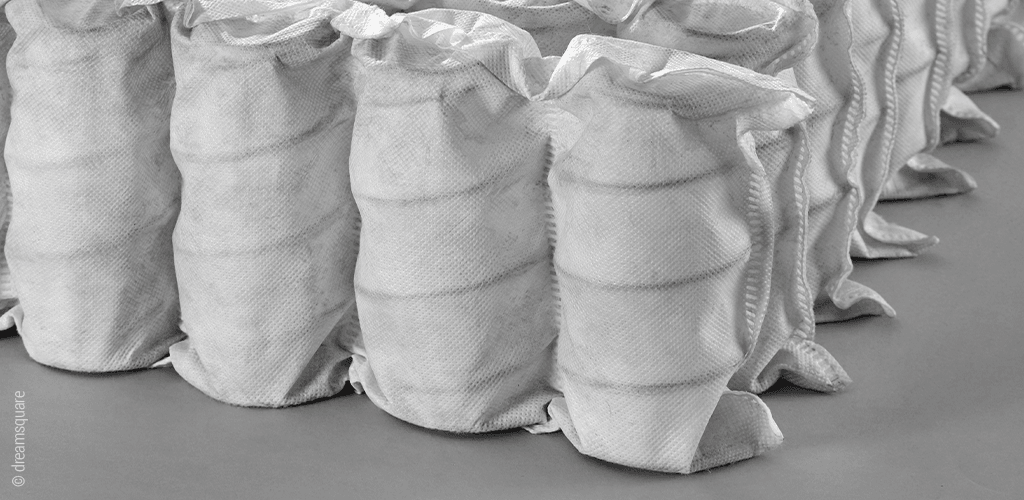
Proces produkcji rdzenia sprężynowego
Rdzenie sprężynowe były stosowane na długo przed wynalezieniem pianek i lateksu. Przez lata powstało wiele różnych metod ich produkcji. Dawniej wykonywano je ręcznie, jednak obecnie większość procesu produkcyjnego jest zautomatyzowana. Mimo to niektóre etapy nadal wymagają pracy ręcznej. Na przykład sprężyny w materacach kieszeniowych są wprawdzie wszywane w materiałowe kieszenie za pomocą maszyny do szycia, ale nadal wymaga to ręcznego prowadzenia materiału. Gotowy rdzeń sprężynowy jest następnie ręcznie umieszczany w otulinie z pianki, a rzadziej z końskiego włosia lub owczej wełny.
Rdzeń lateksowy
Rodzaje rdzeni lateksowych
W produkcji materacy rozróżnia się lateks naturalny i syntetyczny. W rzeczywistości większość rdzeni lateksowych stanowi mieszanka obu tych materiałów. Naturalny lateks jest droższy i bardziej miękki, podczas gdy syntetyczny jest tańszy i bardziej sprężysty. Proporcje tych składników mają wpływ na właściwości końcowego produktu.
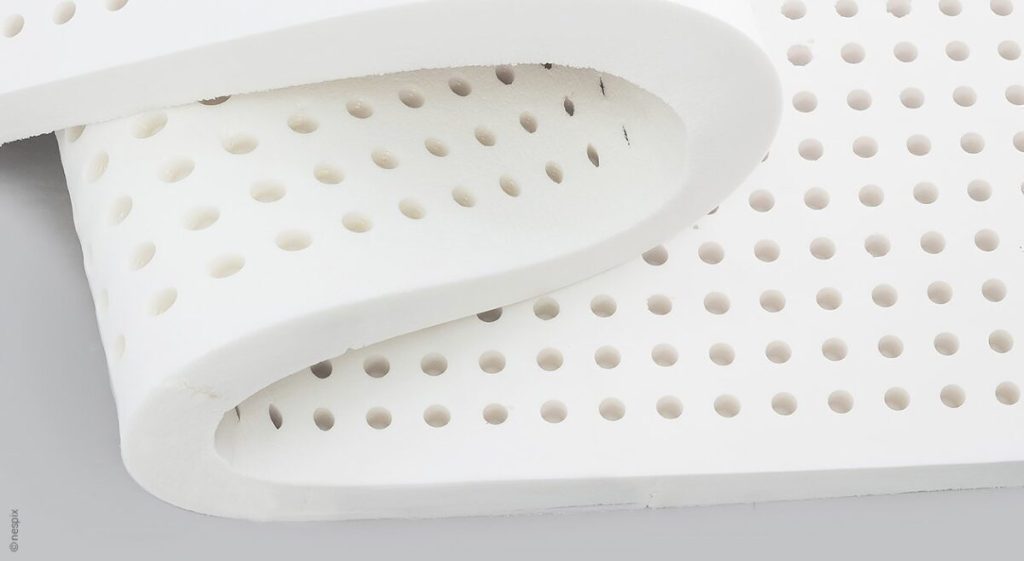
Proces produkcji rdzenia lateksowego
Lateks naturalny pochodzi z soku drzewa kauczukowego, a syntetyczny jest wytwarzany z ropy naftowej. Podobnie jak w przypadku pianki, lateks jest spieniany, ale w przeciwieństwie do niej – formowany indywidualnie. W temperaturze około 120°C lateks jest wulkanizowany, co nadaje mu charakterystyczną elastyczność. Najlepsze rdzenie lateksowe są dodatkowo poddawane procesowi Talalay, który polega na szybkim zamrażaniu do -30°C i ponownym podgrzewaniu, co poprawia wentylację i trwałość.
Pokrowiec – ostatni etap w produkcji materaca
Pokrowiec materaca może znacząco wpłynąć na jego właściwości. Tradycyjnie w materacach sprężynowych stosuje się grube, pikowane pokrowce, które zwiększają stabilność i komfort. W nowoczesnych materacach piankowych i lateksowych używa się elastycznych materiałów, które nie ograniczają ergonomicznych właściwości rdzenia. Pokrowiec HyBreeze® w materacu BODYGUARD® ma strukturę 3D, co zwiększa jego oddychalność.
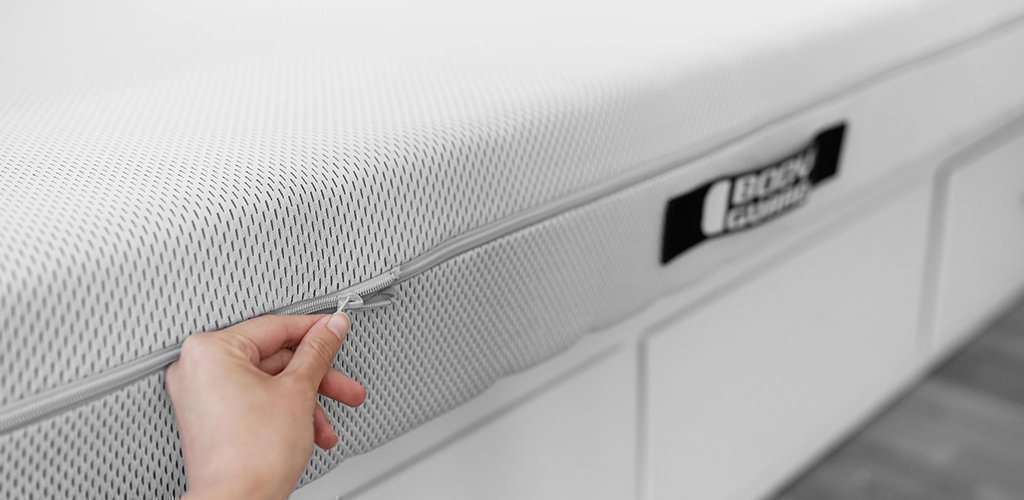
Tkaniny wykorzystywane w produkcji materacy są obecnie wytwarzane maszynowo, ale niektóre detale wciąż wymagają pracy ręcznej. Podobnie jak w przemyśle tekstylnym, producenci materacy mogą wybierać spośród dostępnych tkanin lub projektować własne wzory. Zautomatyzowane przemysłowe maszyny do szycia, sterowane komputerowo, są w stanie produkować ten sam materiał w niemal nieograniczonych ilościach zgodnie z wcześniej ustalonym wzorem. Bardziej skomplikowane szwy pokrowców materacy są jednak nadal wykonywane ręcznie przy użyciu maszyn do szycia.
Łączenie pokrowca z materacem może odbywać się w pełni automatycznie. Z tego powodu nowe materace często posiadają tzw. “skarpetę” materacową, czyli cienką warstwę materiału nałożoną na rdzeń materaca. Jest ona zakładana maszynowo, co ułatwia późniejsze nałożenie właściwego pokrowca przez kolejną maszynę. Po zakończeniu procesu produkcji materaca skarpeta ta nie ma już żadnego praktycznego zastosowania i może zostać bez obaw usunięta.